Materials are required for various purposes. Construction materials such as cement, stone, etc., are used to build structures. Certain materials, such as metal, wood, etc., are employed to make items such as coins, windows, etc. Many different materials exist, such as plastics, paper, silk, water, and soil. These are used for important purposes.
Many businesses depend on materials to function. Without these, they will not be able to operate. Handling and managing these materials can be difficult, but it is necessary for a company to function effectively. Material lists are useful documents that can help out here.
What are material lists?
These are documents that include a list of materials required for a project. The template contains details about the materials available.
Construction Material List
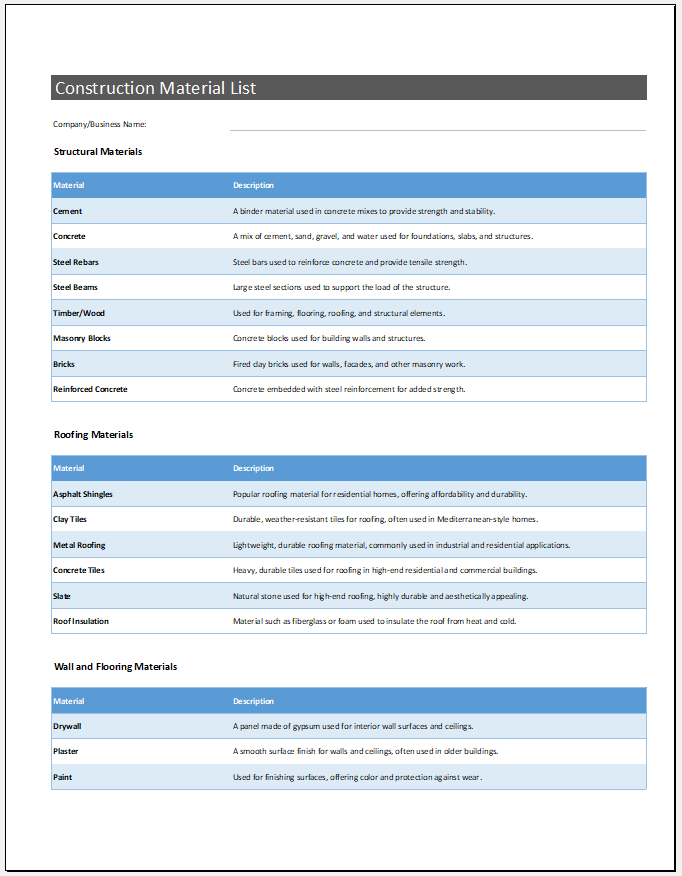
Excel Worksheet Files
Manufacturing Material List
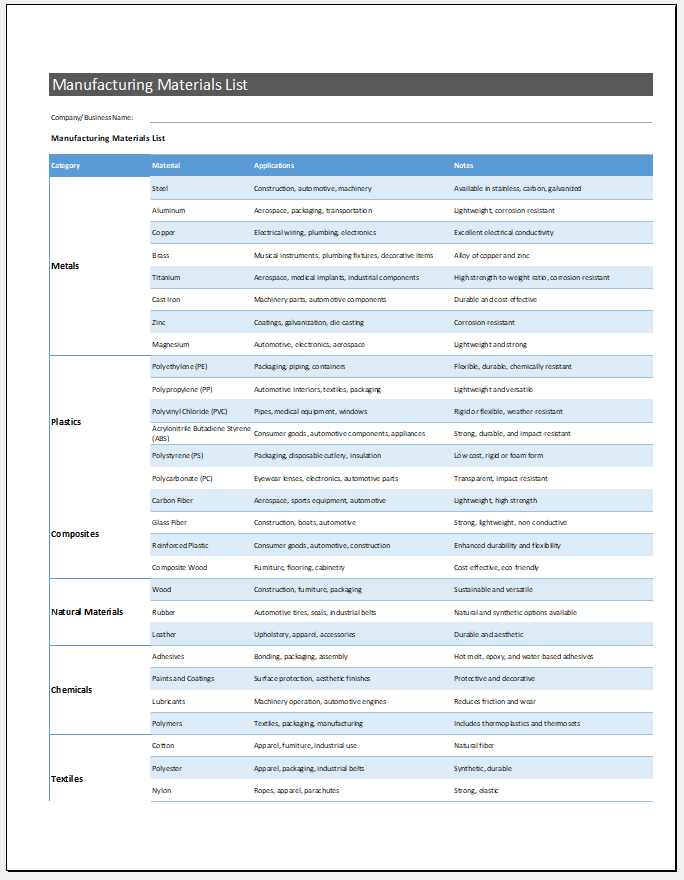
Excel Worksheet Files
Electrical & Electronics Components Material List
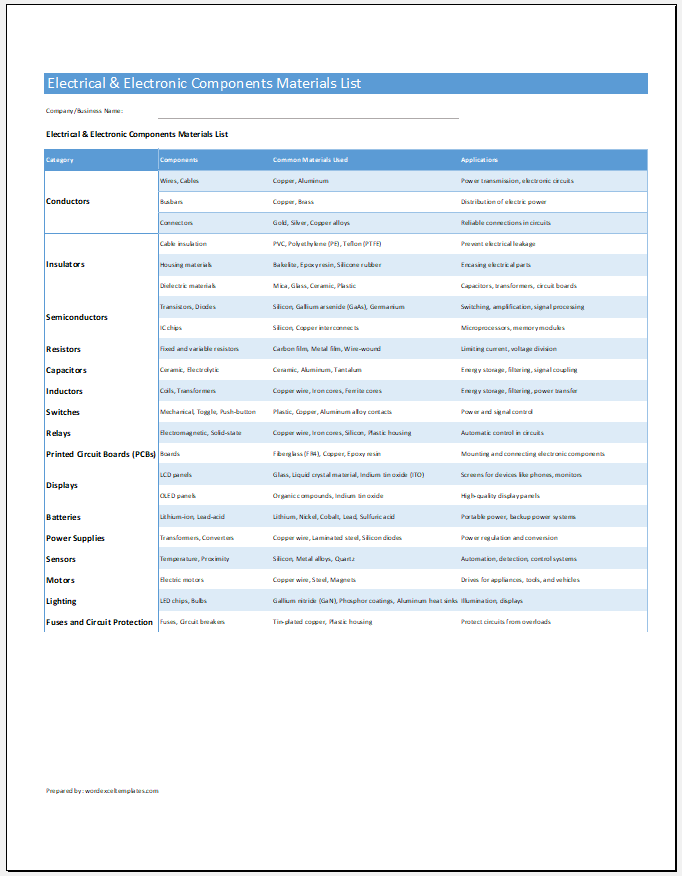
Excel Worksheet Files
Medical Material List
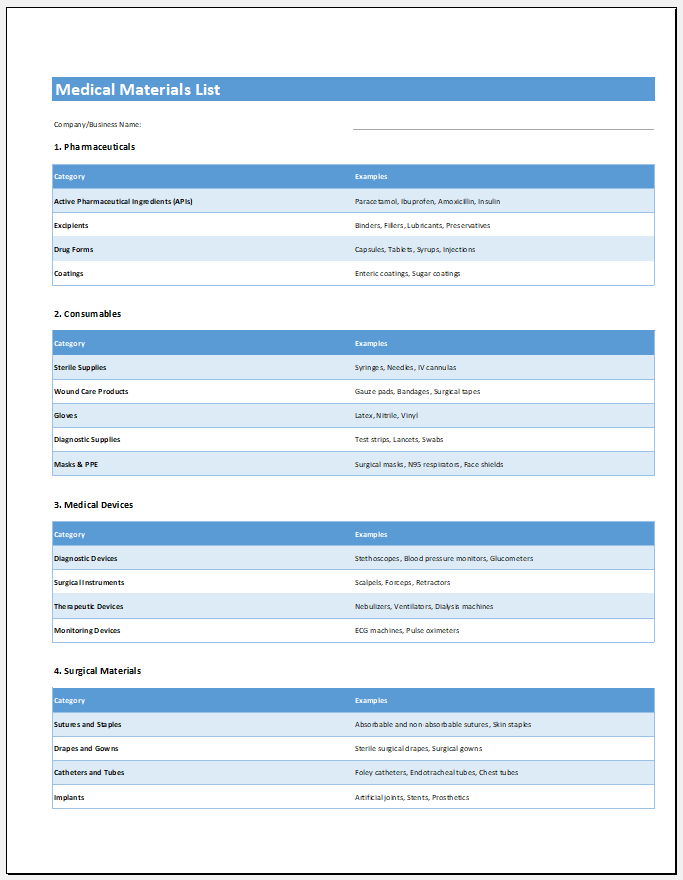
Excel Worksheet Files
Food Production Material List
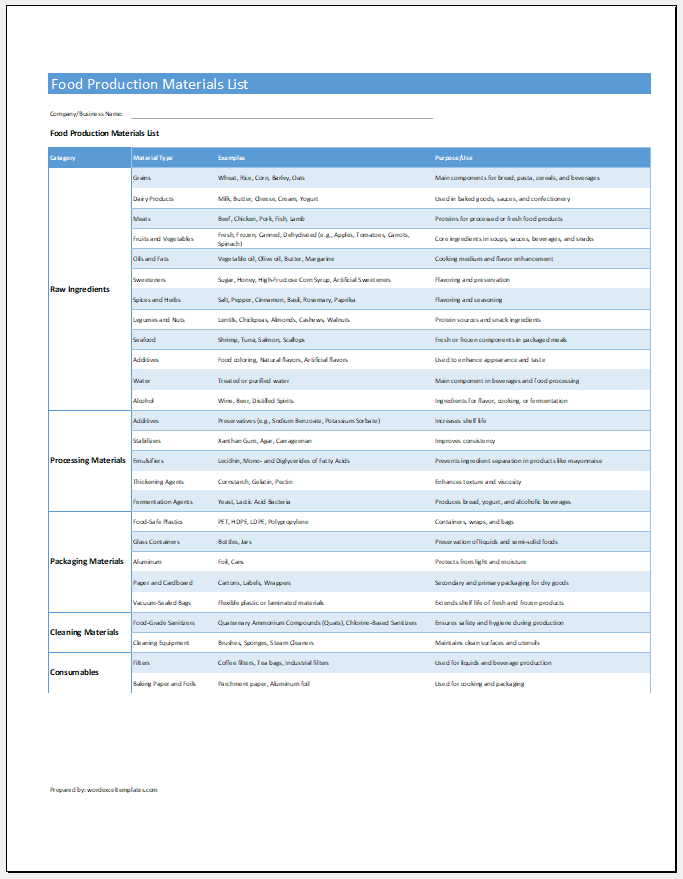
Excel Worksheet Files
Textile Industry Material List
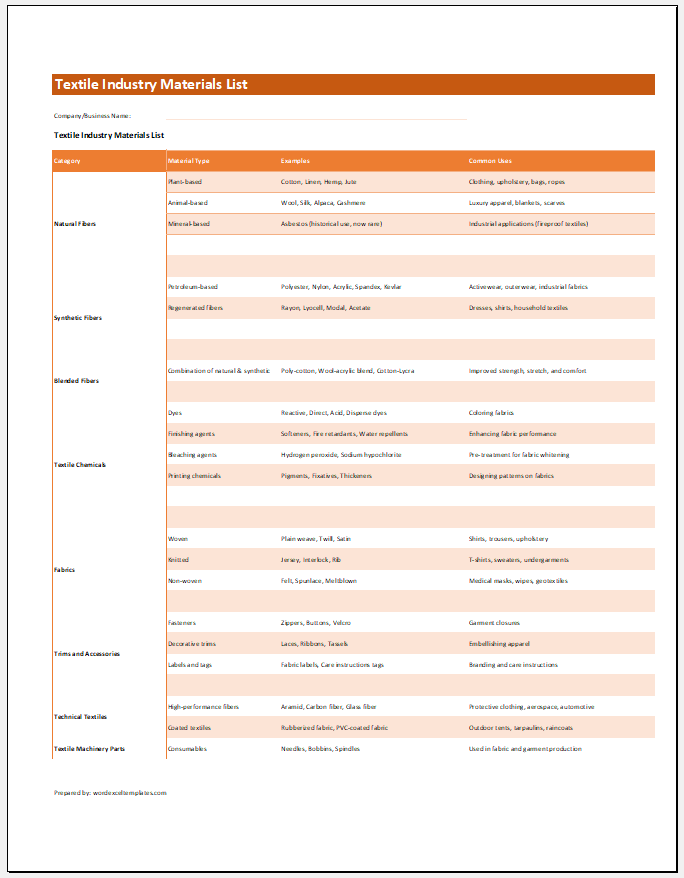
Excel Worksheet Files
Furniture Manufacturer Material List
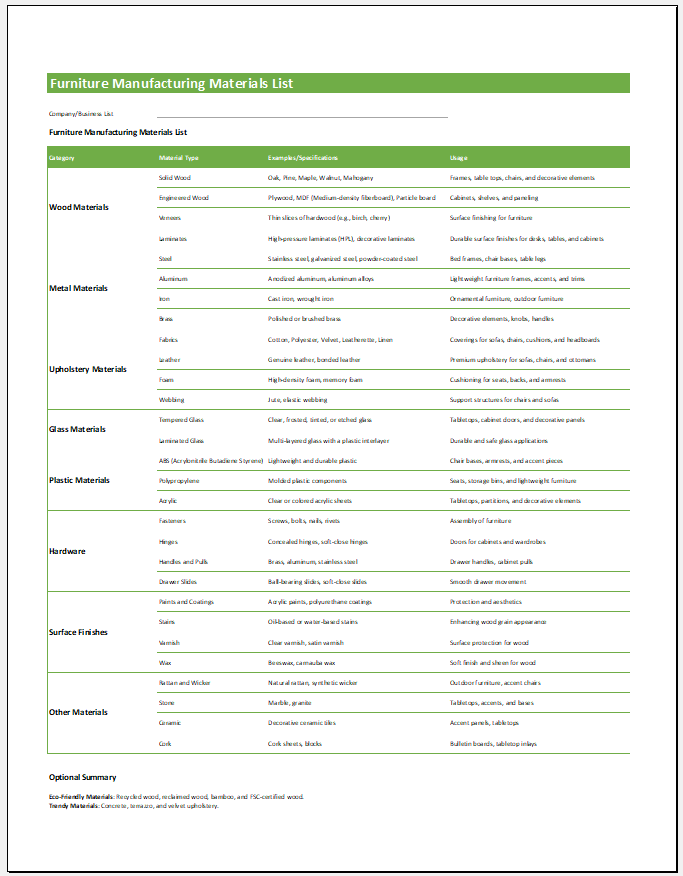
Excel Worksheet Files
The lists let one know which materials are in stock to be used when needed. They will include important details about the materials, such as their cost, vendor details, how many are available, etc. Therefore, they will let you know which materials are available and which must be gotten.
It depends on what you are making the list for. It may be for construction, work orders, business purposes, etc., and it will be made for this reason. There are some general points to remember when creating a material list. These are explained below:
Simple to use list:
The list must be easy to understand and use by those who need to do this. It should have a heading, such as “Material List.” On the list, mention your company’s name and note its contact information. You can also include the date on the document.
Create table:
If the information is in a table format, it will be easy to understand. There should be a column for “Material Name.” Under this, the name of the material will be noted down. A column for “Description” is essential to describe the material and let people know about it precisely. A column for “Quantity” will state the amount of material available.
A column for “Unit Cost” will tell you how much the material costs per unit. You can also have a column for “Vendor” to note who you bought the item from so that you will know who to get it from if you want to repurchase it.
If there are any issues with the material, you will know who you got this from if this information is included in the table. A column for total will mention the total price of the material. According to what the list has been made for, you will include the relevant details on it.
It helps you effectively track materials.
These lists are important as they let you know which materials are present when required and whether these are in the right quantities. This helps reduce production delays and inventory inaccuracies. When you include details about the materials, such as their cost, you will know how much you are spending on them and whether they are helping you make a profit for your company.
When you know which materials are available, you will not order more of them and, therefore, can limit waste. You will not need to find a place to store the extra materials, as you will get the correct quantity. Production can be streamlined when you have the suitable materials available when required and do not need to buy them now.
The list helps a company effectively track and manage materials so they are not wasted and profitable for the business. If you sell materials and have a list, you will know which materials you need to get so that they are available to customers when needed. Operations can occur more efficiently when there is no time delay due to insufficient materials.
- Quarterly Tax Payment Tracker
- Payroll Tracker for Excel
- Delivery Route Optimization Worksheet
- Energy Consumption Monitoring Worksheet
- Return on Investment (ROI) Calculator
- Investment Portfolio Tracker
- Equipment Utilization Worksheet
- Emissions Monitoring Worksheet
- Monthly Utility Consumption Worksheet
- Sales Tax Calculation Sheet
- Fixed Asset Register Template
- Advance Salary Tracker
- Benefits and Deductions Worksheet
- Capital Expenditure Tracker Template
- Departmental Budget Allocation Sheet